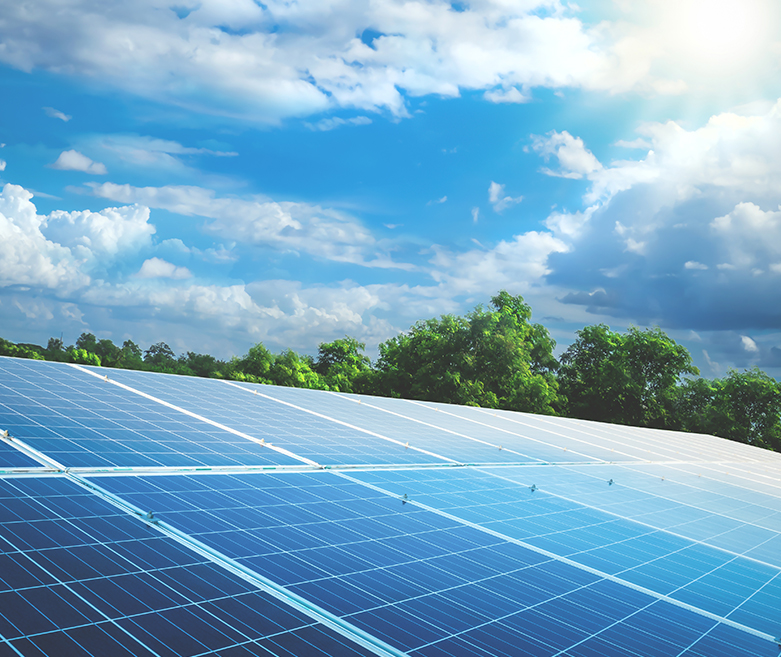
We’re committed to a sustainable future
Smart is fully committed to achieving a greener environment and so every aspect of our activities, from the procurement of raw materials to the delivery of finished goods, is conducted in accordance with sound environmental practices and in line with UK and EU environmental regulations and legislation.
Our 360o approach to a sustainable future for extrusion in the UK
Throughout our development, environmental considerations have been central to our planning, and to help formalise our processes and procedures, in 2011 we achieved ISO 14001:2004 Environmental Management Systems certification.
Our goal is to achieve a completely carbon-neutral production operation, which we intend to achieve through a combination of continued investment in efficient machinery; the operation of effective environmental management systems; the use of waste capture and recycling techniques and the introduction of sustainable power generation from natural resources.

Find out why aluminium is the greenest metal on Earth
Durable, lightweight and resistant to both corrosion and pollutants, aluminium products have a life cycle measured in decades rather than years.
Our ambition is to protect our environment and reduce our impact
We also work extremely closely and collaboratively with our local supply chain to improve the CO₂ output through the value chain. The suppliers we work with provide us some of the lowest production CO₂ footprint in the world, whilst also enabling us to recycle 100% of our waste. In 2022 we received 60% of our raw material with our own recycled content.
In 2022, the recycle content of our aluminium billet was 62%, with 100% of all our aluminium waste being recycled.
We continue to invest in efficient machinery, effective environmental management systems and waste capture and recycling systems, as well as the use of sustainable power generation.
In line with our commitment to sustainable manufacture, our finishing plant incorporates a number of environmental features. For example, our rainwater capture system holds up to 900,000 litres of collected rainwater which is filtered for cleaning prior to use in the pre-treatment process – the alkaline-based pre-treatment process is 100% chromate free.

100% of our billet is responsibly sourced
To ensure we consistently deliver aluminium extrusions to the highest quality standards, we source aluminium billet only from three of the world’s leading suppliers, Emirates Aluminium, Dubai Aluminium and Hydro Aluminium.
The first company of its kind to be awarded 5 BSI standards
Operating extensive test regimes, we are committed to consistently achieving high standards of quality and were the UK’s first systems company to achieve five separate ISO standards.
We are the greenest operation of its kind in the UK
Through continued investment, our state-of-the-art, 60,000m² manufacturing facility in the south west of England is now home to four extrusion presses and four powder coat paint lines, as well as a wide range of machining and finishing equipment. Our new fourth press is our most energy efficient yet, it uses 33% less energy, and reflects our objective of continually innovating to provide a more efficient production facility.
Already the largest single-site extrusion plant in the UK, the installation of our fourth press allows us to provide both a dedicated resource and guaranteed capacity for all our extrusion customers.
With our extrusion, machining, finishing and packaging processes all on one site, as well as our own fleet of delivery vehicles, we have complete control of every customer order, from receipt right through to final delivery.
We also recently invested in a completely new die storage system which allows us to have 99% of our dies ready to run on demand when the customer requires. Our service schedule of the dies allows us to store 50% of dies pre-filled before they need cleaning with caustic solution (meaning 50% less waste) and dies can be sent to our presses within hours, not days.
Our caustic waste, which is harmful to the environment, and which would once have been sent to landfill at end of life, is now re-used, with a local business re-using the waste solution.
The most advanced facility of its kind
Smart is fully committed to achieving a greener environment and so every aspect of our activities, from the procurement of raw materials to the delivery of finished goods, is conducted in accordance with sound environmental practices and in line with UK and EU environmental regulations and legislation.

Waste Capture and Recycling
Our waste capture and recycling techniques are integral to our sustainable manufacturing ethos – and our drive to achieving carbon neutrality.

Working Towards Carbon Neutrality
We aim to achieve carbon-neutral production through continued investment in efficient machinery, waste capture and recycling techniques and sustainable power generation.
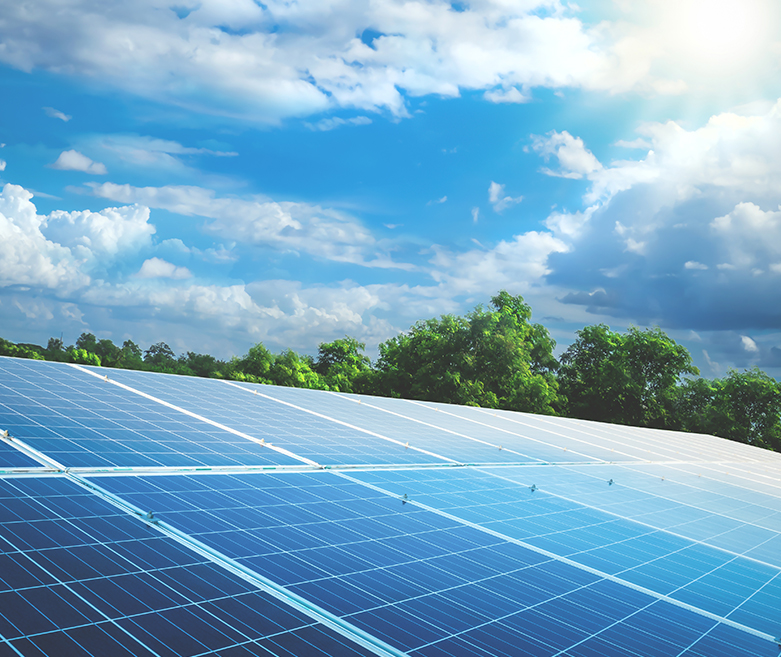
Sustainability
With the greenest manufacturing operation of its kind in the country, sustainability is a crucial consideration across all our business operations and plan to become carbon neutral.